1
HCBS Sector 102 Gurugram: Your Dream House is Waiting for You
2
Flights to Dubai | Your Comprehensive Guide for UK Travellers
3
Express Entry 2025: Significant Shifts and Forecasts for Immigration to Canada
4
Decking Calculator: The Key to Planning Your Perfect Outdoor Space
5
Quality Selections: Your Trusted Destination for High-Quality Products and Exceptional Customer Service
6
Essential Online Privacy Tips for a Secure Digital Life
7
Sepatu Compass: Sepatu Impian Si Kecil, Cerita Haru dan Bahagia
8
What Is Social Media Content And How Is It Created?
9
How to Prepare for CAT Exam: Study Tips
10
Why BM Coder is the Best Laravel Development Company in India
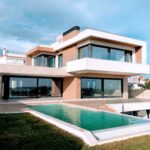
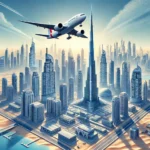
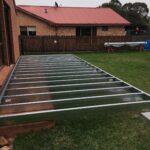
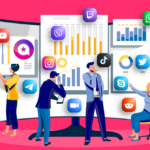